Free Shipping Within USA | 1-year Warranty | Self Pick Up
Steel Tracks vs. Rubber Tracks: What is the Difference?
Mini excavators have become indispensable tools across a range of industries, from construction to landscaping. These compact excavators are prized for their ability to operate in tight spaces where larger equipment cannot tread. However, the efficiency of a mini excavator is highly dependent on its undercarriage system-specifically, the type of tracks it employs. This guide will explore the specific differences between steel tracks and rubber tracks to help you master more knowledge about mini excavators. If you are looking for a mini excavator for sale, understanding the advantages and drawbacks of mini excavator steel tracks and rubber tracks can help you make an informed purchase decision.
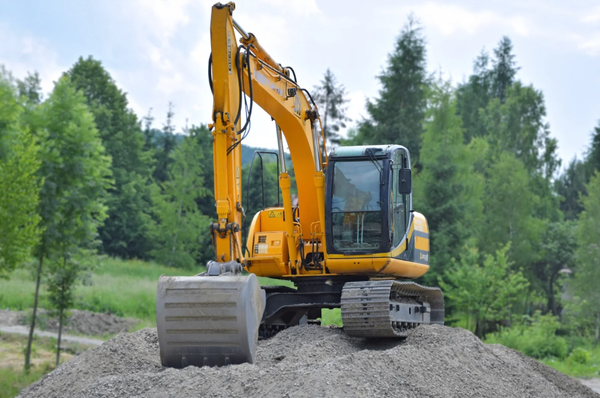
What are Rubber Tracks for Mini Excavators?
Rubber tracks for mini excavators are constructed from high-quality rubber compounds which are often reinforced with continuous steel cords or embedded cables. These mini excavator rubber tracks are designed for flexibility and minimal ground disturbance, making them ideal for various applications, particularly in urban or landscaped environments.
Common Applications
- Landscaping and Urban Construction: Rubber excavator tracks are preferable for projects within urban settings or on landscaped properties where ground preservation is critical.
- Indoor Operations: Since rubber tracks do not leave marks or cuts on the surface, they are also perfect for indoor use where steel tracks may damage the surface.
Soft Terrain: Rubber excavator tracks can distribute the weight of the mini excavator more evenly, reducing the risk of sinking in muddy or sandy conditions.
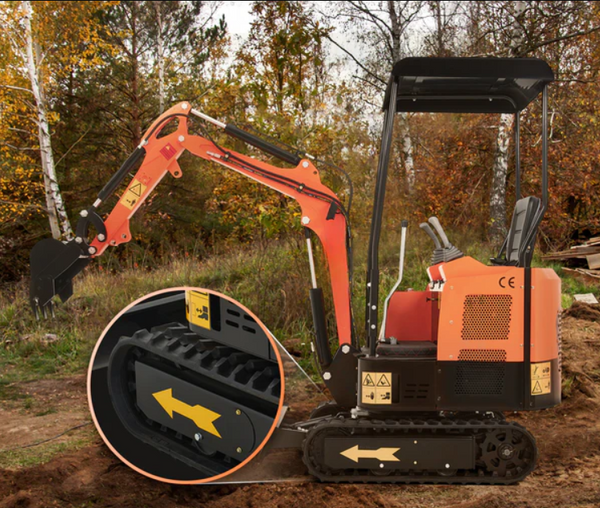
Advantages of Rubber Tracks
Reduced Surface Impact: Compared to steel tracks, the softer material causes less damage to concrete, asphalt, and other sensitive surfaces.
Lower Noise Levels: Rubber tracks operate much quieter, which is beneficial in noise- sensitive areas like residential zones or hospitals.
Improved Traction: The flexibility of rubber tracks allows for better grip and handling on slippery or uneven surfaces.
Drawbacks of Rubber Tracks
Wear and Tear: Rubber tracks may wear out faster than steel tracks, especially when used frequently on abrasive surfaces.
- Higher Replacement Frequency: Rubber tracks need to be replaced frequently. This can increase operational costs over the lifespan of the mini excavator.
What are Steel Tracks for Mini Excavators?
Steel tracks for mini excavators usually consist of interconnected steel plates or pads and are known for their strength and durability. These tracks are suitable for mini excavators operating in harsh environments where maximum durability is required.
Primary Uses
Heavy-duty Construction Sites: Steel tracks are ideal for rugged terrains like those
found in large-scale construction and demolition sites.
Rocky or Abrasive Environments: The durability of steel tracks can make them suitable for areas with sharp debris.
Stoop or Unstable Terrains: The weight and sturdiness of steel tracks provide better stability on slopes and uneven landscapes.
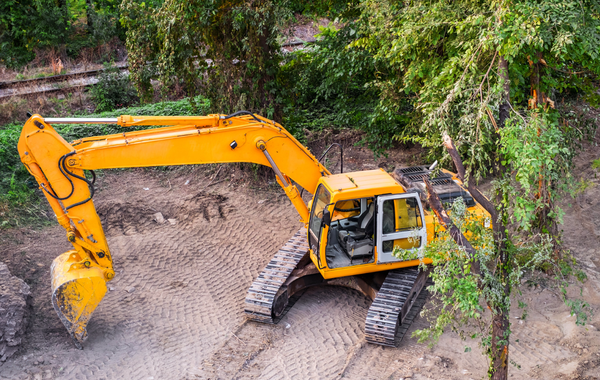
Benefits of Steel Tracks
Longevity: Steel tracks generally last longer than rubber tracks under similar
conditions, but particularly in harsh environments. Greater Traction: The rigid construction enhances the mini excavator’s stability and traction on challenging sürfaces.
Disadvantages of Steel Tracks
Potential for Surface Damage: Steel tracks can significantly damage paved surfaces, making them less ideal for residential or urban construction sites. Increased Noise and Vibration: They tend to be noisier and create more vibrations
during operation, which could lead to faster wear of the mini excavator’s components. Higher Maintenance Needs: Steel tracks require regular maintenance to prevent rust and corrosion, potentially increasing long-term operational costs.
Steel Tracks vs. Rubber Tracks: A Comprehensive Analysis
Choosing between steel tracks and rubber tracks for mini excavators involves considering a variety of factors including the specific environment and operational needs. Here is a detailed comparison based on several criteria:
Durability and Maintenance Steol tracks are unrivaled in terms of durability, especially in abrasive conditions such as quarries or demolition sites. They are less susceptible to damage from sharp objects and extreme conditions. However, this durability comes with the need for regular maintenance to prevent rust and joint wear. Rubber tracks, while less durable in harsh environments, require minimal maintenance and are better suited for urban or landscaped areas where surface damage needs to be minimized.
Traction and Stability: Steel tracks provide superior traction in loose or uneven terrains, making them ideal for steep grades and unstable ground. Rubber tracks, on the other hand, offer enhanced stability on soft or sensitive surfaces, reducing the risk of damage to turf or paved areas.
Noise and Vibration: Operations in residential or noise-sensitive areas benefit from rubber tracks, which significantly reduce noise and vibration compared to steel tracks. This can be a critical factor when working in urban settings or in close proximity to inhabited areas.
Cost-Effectiveness: Initial Investments in steel tracks are higher, but their longer lifespan can make them more cost-effective over time for heavy-duty operations. Rubber tracks might have a lower upfront cost but might need more frequent replacements depending on the usage intensity and conditions.
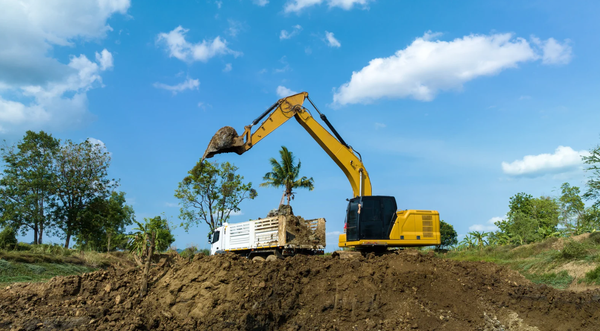
Care Tips for Steel Tracks and Rubber Tracks for Mini Excavators
Proper maintenance of mini excavator tracks not only extends their lifespan but also ensures optimal performance and rellability. Here are specific care tips for both steel tracks and rubber tracks:
For Rubber Tracks
Regular Cleaning: After each use, remove debris and dirt from the tracks. This prevents buildup that can cause premature wear or damage. Pay particular attention to cleaning out any materials lodged within the track undercarriage.
Avold Harsh Chemicals: Use only manufacturer-recommended cleaning agents. Harsh chemicals can degrade rubber, reducing track life.
Storage Considerations: When not in use, store your mini excavator in a cool, dry place to prevent the rubber from becoming brittle and cracking, especially in cold environments.
For Steel Tracks
Lubrication: Regularly lubricate the pins and bushings to reduce friction, which can cause excessive wear. Use the lubrication type and schedule recommended by the manufacturer.
Rust Prevention: Apply coatinga or sprays that inhibit rust, especially if operating in wet conditions or stering outdoors. Keeping the tracks dry and clean also helps provent rust.
Inspection for Wear: Inspect tracks for signs of bending, cracking, or excessive In the links. Replace any damaged or worn parts promptly to maintain the structural Integrity of the track system.
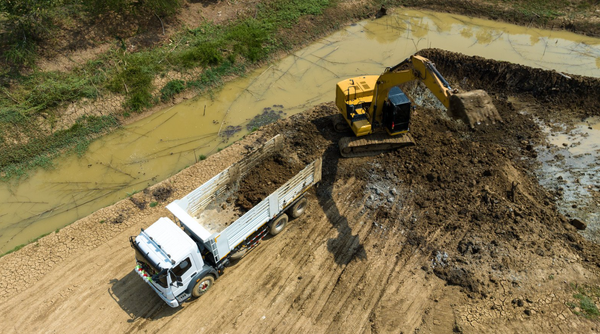
In the debate of steel tracks vs. rubber tracks, the best choice depends heavily on specific operational needs and environmental considerations. Each type has its advantages in certain scenarios, and understanding these can significantly enhance both operational elliciency and compliance with environmental standards. For those in the markat looking for mini excavators for sale, weighing these factors carefully will ensure you select the track type that offers the best balance of performance, cost, and environmental impact.